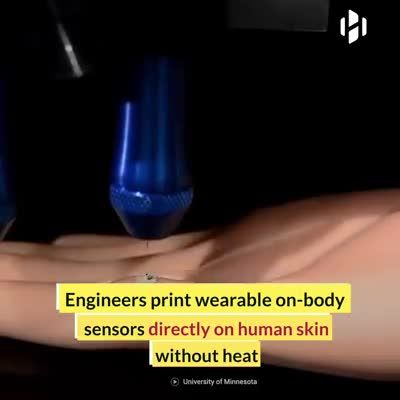
Category: wearables
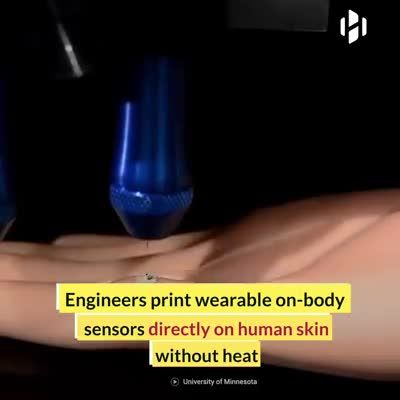
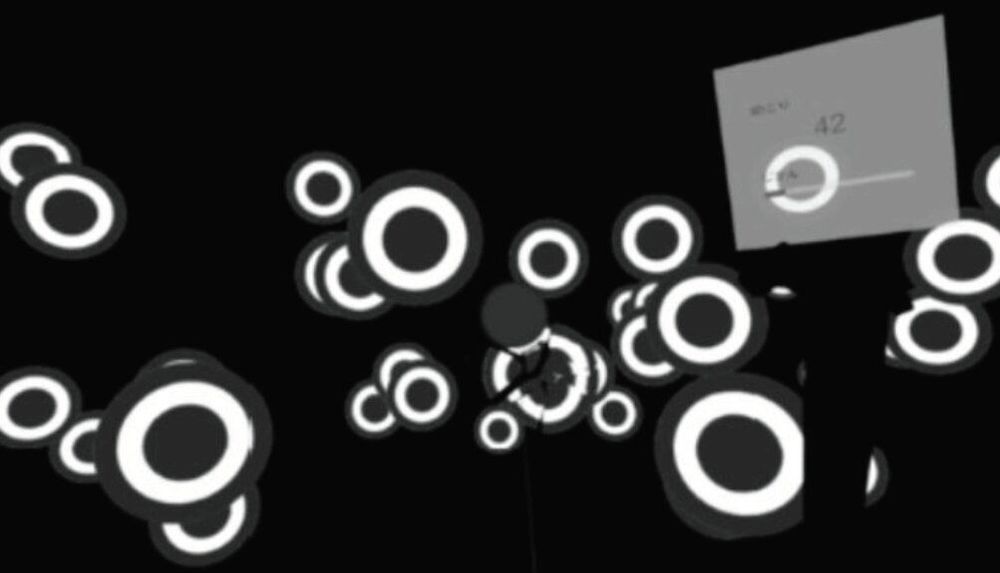
A virtual reality game that integrates tactile experiences using biometric feedback
Over the past few decades, technological advances have enabled the development of increasingly sophisticated, immersive and realistic video games. One of the most noteworthy among these advances is virtual reality (VR), which allows users to experience games or other simulated environments as if they were actually navigating them, via the use of electronic wearable devices.
Most existing VR systems primarily focus on the sense of vision, using headsets that allow users to see what is happening in a game or in another simulated environment right before their eyes, rather than on a screen placed in front of them. While this can lead to highly engaging visual experiences, these experiences are not always matched by other types of sensory inputs.
Researchers at Nagoya University’s School of Informatics in Japan have recently created a new VR game that integrates immersive audiovisual experiences with tactile perception. This game, presented in a paper published in the Journal of Robotics, Networking and Artificial Life, uses a player’s biometric data to create a spherical object in the VR space that beats in alignment with his/her heart. The player can thus perceive the beating of his/her heart via this object visually, auditorily and tactually.
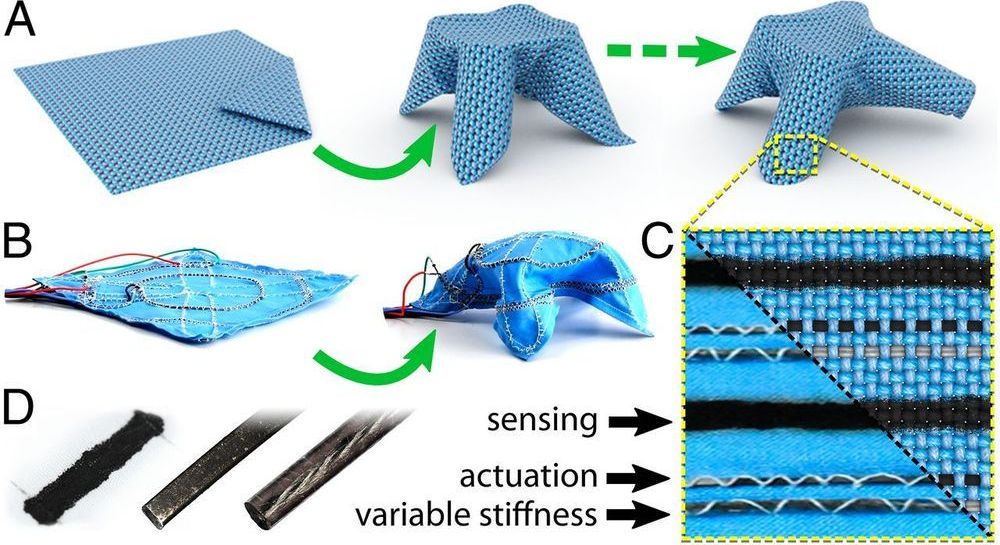
Roboticizing fabric
Fabrics are key materials for a variety of applications that require flexibility, breathability, small storage footprint, and low weight. While fabrics are conventionally passive materials with static properties, emerging technologies have provided many flexible materials that can respond to external stimuli for actuation, structural control, and sensing. Here, we improve upon and process these responsive materials into functional fibers that we integrate into everyday fabrics and demonstrate as fabric-based robots that move, support loads, and allow closed-loop controls, all while retaining the desirable qualities of fabric. Robotic fabrics present a means to create smart adaptable clothing, self-deployable shelters, and lightweight shape-changing machinery.
Fabrics are ubiquitous materials that have conventionally been passive assemblies of interlacing, inactive fibers. However, the recent emergence of active fibers with actuation, sensing, and structural capabilities provides the opportunity to impart robotic function into fabric substrates. Here we present an implementation of robotic fabrics by integrating functional fibers into conventional fabrics using typical textile manufacturing techniques. We introduce a set of actuating and variable-stiffness fibers, as well as printable in-fabric sensors, which allows for robotic closed-loop control of everyday fabrics while remaining lightweight and maintaining breathability. Finally, we demonstrate the utility of robotic fabrics through their application to an active wearable tourniquet, a transforming and load-bearing deployable structure, and an untethered, self-stowing airfoil.
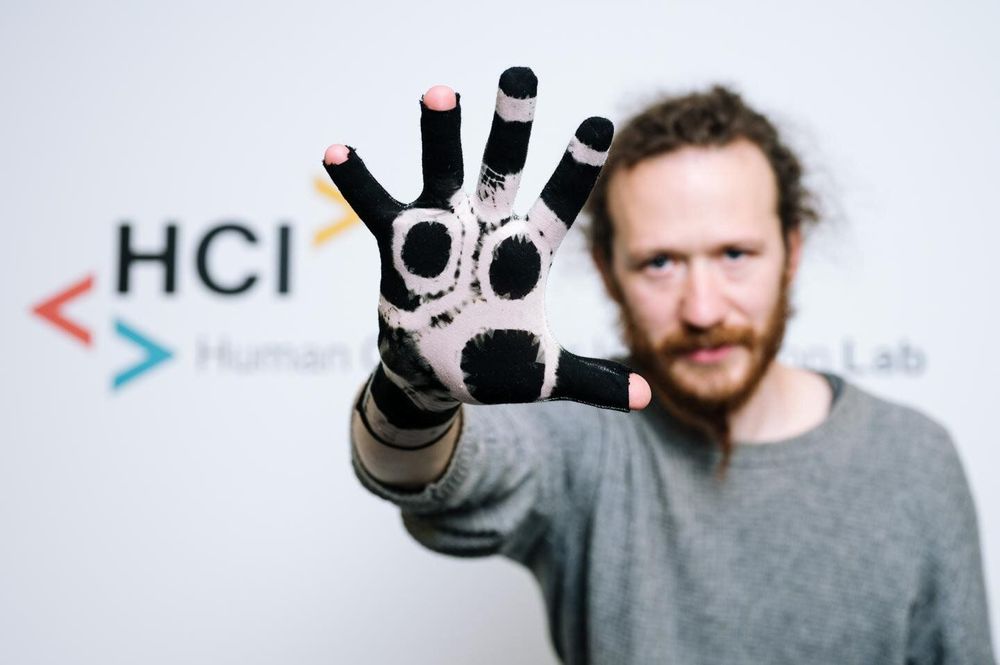
Wearable IT devices: Dyeing process gives textiles electronic properties
“Our goal was to integrate interactive functionalities directly into the fibers of textiles instead of just attaching electronic components to them,” says Jürgen Steimle, computer science professor at Saarland University. In his research group on human-computer interaction at Saarland Informatics Campus, he and his colleagues are investigating how computers and their operation can be integrated as seamlessly as possible into the physical world. This includes the use of electro-interactive materials.
Previous approaches to the production of these textiles are complicated and influence the haptics of the material. The new method makes it possible to convert textiles and garments into e-textiles, without affecting their original properties—they remain thin, stretchable and supple. This creates new options for quick and versatile experimentation with new forms of e-textiles and their integration into IT devices.
“Especially for devices worn on the body, it is important that they restrict movement as little as possible and at the same time can process high-resolution input signals”, explains Paul Strohmeier, one of the initiators of the project and a scientist in Steimle’s research group. To achieve this, the Saarbrücken researchers are using the in-situ polymerization process. Here, the electrical properties are “dyed” into the fabric: a textile is subjected to a chemical reaction in a water bath, known as polymerization, which makes it electrically conductive and sensitive to pressure and stretching, giving it so-called piezoresistive properties. By “dyeing” only certain areas of a textile or polymerizing individual threads, the computer scientists can produce customized e-textiles.
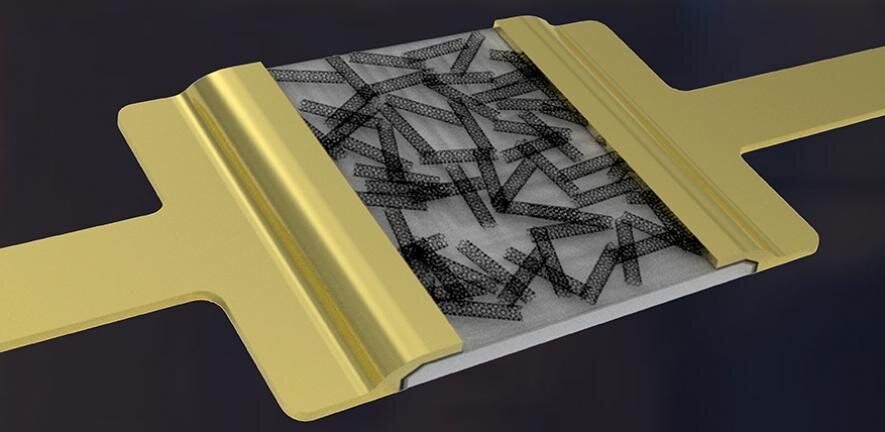
Easy-to-make, ultra-low power electronics could charge out of thin air
Researchers have developed a new approach to printed electronics which allows ultra-low power electronic devices that could recharge from ambient light or radiofrequency noise. The approach paves the way for low-cost printed electronics that could be seamlessly embedded in everyday objects and environments.
Electronics that consume tiny amounts of power are key for the development of the Internet of Things, in which everyday objects are connected to the internet. Many emerging technologies, from wearables to healthcare devices to smart homes and smart cities, need cost-effective transistors and electronic circuits that can function with minimal energy use.
Printed electronics are a simple and inexpensive way to manufacture electronics that could pave the way for low-cost electronic devices on unconventional substrates—such as clothes, plastic wrap or paper—and provide everyday objects with ‘intelligence’.
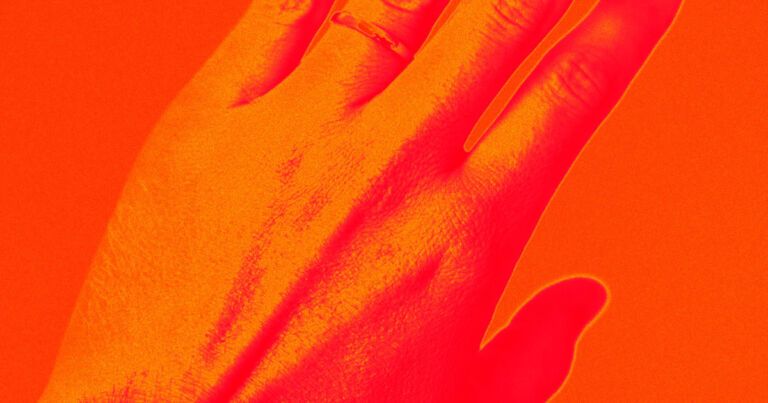
New Wearables Can Be Printed Directly Onto Skin
Colder, Colder…
The process of sintering, or bonding the metals that make up the flexible circuits, usually happens at 572 degrees Fahrenheit.
“The skin surface cannot withstand such a high temperature, obviously,” Penn State engineer and lead author Hanyu “Larry” Cheng said in a press release. “To get around this limitation, we proposed a sintering aid layer — something that would not hurt the skin and could help the material sinter together at a lower temperature.”

What Brain-Computer Interfaces Could Mean for the Future of Work
Imagine if your manager could know whether you actually paid attention in your last Zoom meeting. Or, imagine if you could prepare your next presentation using only your thoughts. These scenarios might soon become a reality thanks to the development of brain-computer interfaces (BCIs).
To put it in the simplest terms, think of a BCI as a bridge between your brain and an external device. As of today, we mostly rely on electroencephalography (EEG) — a collection of methods for monitoring the electrical activity of the brain — to do this. But, that’s changing. By leveraging multiple sensors and complex algorithms, it’s now becoming possible to analyze brain signals and extract relevant brain patterns. Brain activity can then be recorded by a non-invasive device — no surgical intervention needed. In fact, the majority of existing and mainstream BCIs are non-invasive, such as wearable headbands and earbuds.
The development of BCI technology was initially focused on helping paralyzed people control assistive devices using their thoughts. But new use cases are being identified all the time. For example, BCIs can now be used as a neurofeedback training tool to improve cognitive performance. I expect to see a growing number of professionals leveraging BCI tools to improve their performance at work. For example, your BCI could detect that your attention level is too low compared with the importance of a given meeting or task and trigger an alert. It could also adapt the lighting of your office based on how stressed you are, or prevent you from using your company car if drowsiness is detected.
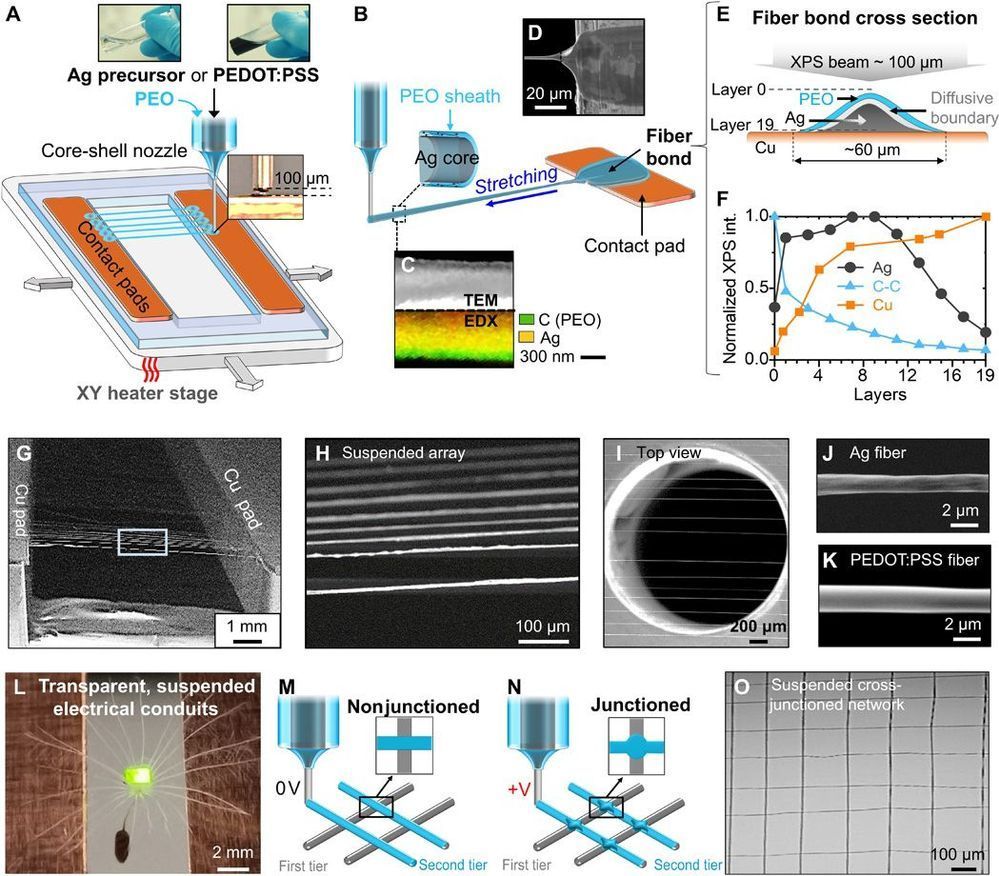
Inflight fiber printing toward array and 3D optoelectronic and sensing architectures
Scalability and device integration have been prevailing issues limiting our ability in harnessing the potential of small-diameter conducting fibers. We report inflight fiber printing (iFP), a one-step process that integrates conducting fiber production and fiber-to-circuit connection. Inorganic (silver) or organic {PEDOT: PSS [poly(3,4-ethylenedioxythiophene) polystyrene sulfonate]} fibers with 1- to 3-μm diameters are fabricated, with the fiber arrays exhibiting more than 95% transmittance (350 to 750 nm). The high surface area–to–volume ratio, permissiveness, and transparency of the fiber arrays were exploited to construct sensing and optoelectronic architectures. We show the PEDOT: PSS fibers as a cell-interfaced impedimetric sensor, a three-dimensional (3D) moisture flow sensor, and noncontact, wearable/portable respiratory sensors. The capability to design suspended fibers, networks of homo cross-junctions and hetero cross-junctions, and coupling iFP fibers with 3D-printed parts paves the way to additive manufacturing of fiber-based 3D devices with multilatitude functions and superior spatiotemporal resolution, beyond conventional film-based device architectures.
Small-diameter conducting fibers have unique morphological, mechanical, and optical properties such as high aspect ratio, low bending stiffness, directionality, and transparency that set them apart from other classes of conducting, film-based micro/nano structures (1–3). Orderly assembling of thin conducting fibers into an array or three-dimensional (3D) structures upscales their functional performance for device coupling. Developing new strategies to control rapid synthesis, patterning, and integration of these conducting elements into a device architecture could mark an important step in enabling new device functions and electronic designs (4, 5). To date, conducting micro/nanoscaled fibers have been produced and assembled in a number of ways, from transferring of chemically grown nanofibers/wires (6, 7), writing electrohydrodynamically deposited lines (8, 9), to drawing ultralong fibers (10, 11), wet spinning of fibers (12–14), and 2D/3D direct printing (15–18).
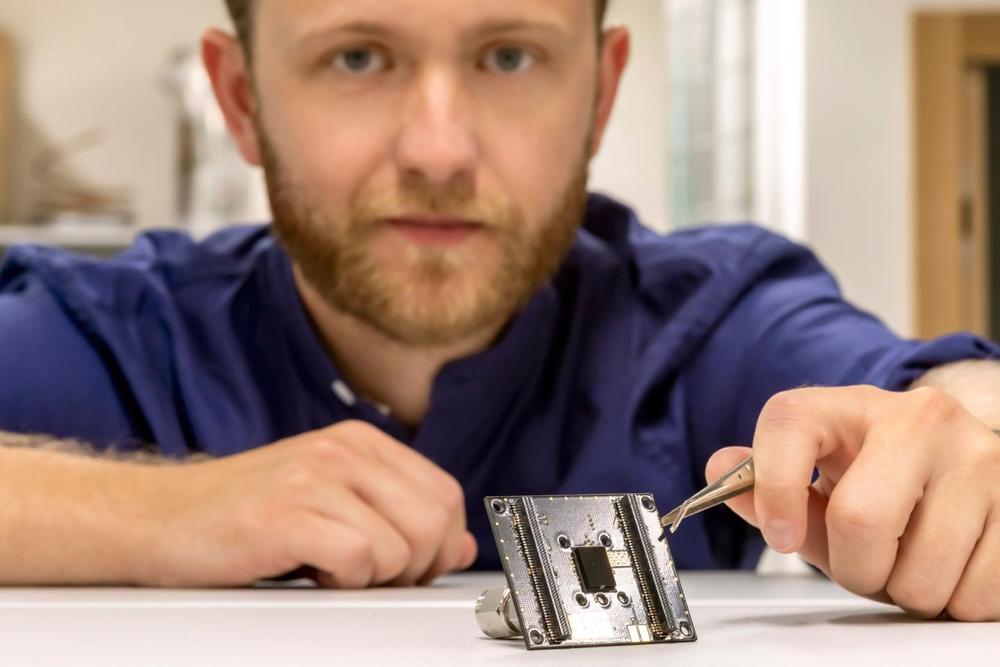
World’s smallest fine particle air pollution sensor fits inside a phone
Air pollution involving very fine dust, such as PM2.5 particles, poses a serious threat to human health. Scientists in Austria have developed what they call the smallest particle sensor in the world, designed specifically to detect these harmful pollutants and offer a highly localized picture of air quality by being integrated into wearables and mobile devices.
According to the World Health Organization, air pollution contributes to more than four million premature deaths each year. While PM10 particles with a diameter of 10 microns or less can also make their way into their lungs, the finer PM2.5 particles are even more dangerous, as they can penetrate the lung barrier, slip into the blood stream and, through chronic exposure, cause severe forms of cardiovascular and respiratory disease, along with other health problems.
Concentrations of PM2.5 particles can be gauged through monitoring stations positioned around cities and regions, in fact the US Environmental Protection Agency uses a nationwide network of these stations to track air quality trends. But scientists from Austria’s Graz University of Technology (TU Graz) have been working on a more cost-effective, compact and versatile solution that can alert individual users of dangerous conditions in real time.
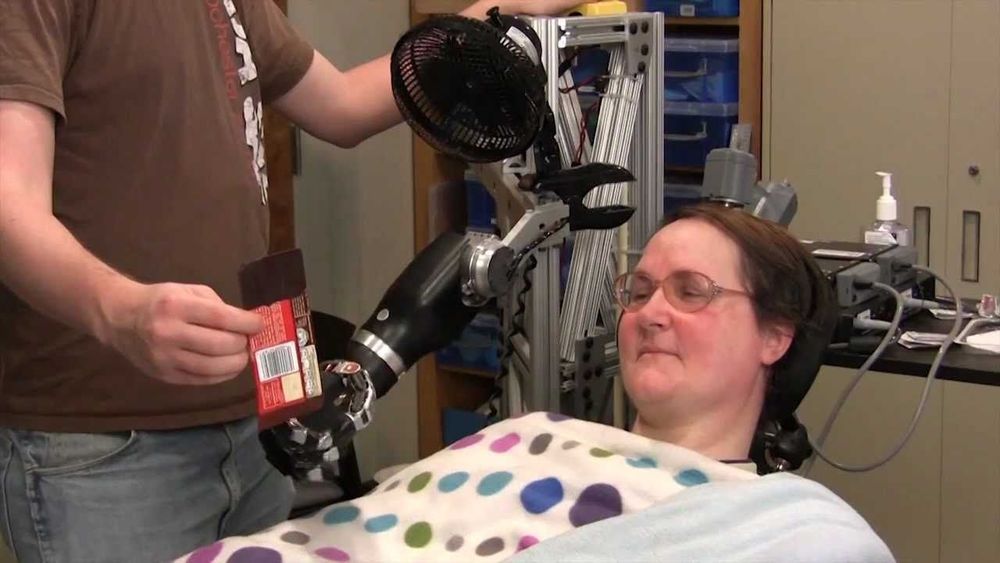
The brain-computer interface is coming, and we are so not ready for it
Are you ready?
“if you were the type of geek, growing up, who enjoyed taking apart mechanical things and putting them back together again, who had your own corner of the garage or the basement filled with electronics and parts of electronics that you endlessly reconfigured, who learned to solder before you could ride a bike, your dream job would be at the Intelligent Systems Center of the Applied Physics Laboratory at Johns Hopkins University. Housed in an indistinct, cream-colored building in a part of Maryland where you can still keep a horse in your back yard, the ISC so elevates geekdom that the first thing you see past the receptionist’s desk is a paradise for the kind of person who isn’t just thrilled by gadgets, but who is compelled to understand how they work.”
Then there are the legal questions: Can the cops make you wear one? What if they have a warrant to connect your brain to a computer? How about a judge? Your commanding officer? How do you keep your Google Nest from sending light bulb ads to your brain every time you think the room is too dark?
A wearable device that can decode the voice in your head is a way’s off yet, said Jack Gallant, professor of psychology at University of California, Berkeley and a leading expert in cognitive neuroscience. But he also said, “Science marches on. There’s no fundamental physics reason that someday we’re not going to have a non-invasive brain-machine interface. It’s just a matter of time.
”And we have to manage that eventuality.”