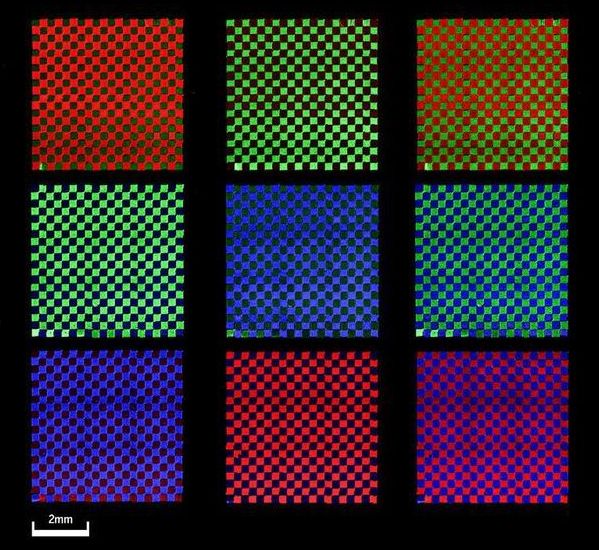
In solar cells, the cheap, easy to make materials called perovskites are adept at turning photons into electricity. Now, perovskites are turning the tables, converting electrons into light with an efficiency on par with that of the commercial organic light-emitting diodes (LEDs) found in cellphones and flat screen TVs. And in a glimpse of how they might one day be harnessed, researchers reported last week in Science Advances that they’ve used a 3D printer to pattern perovskites for use in full-color displays.
“It’s a fantastic result, and quite inspirational,” says Richard Friend, a physicist at the University of Cambridge in the United Kingdom whose team created the first perovskite LED in 2014. The result raises hopes that the computer screens and giant displays of the future will consist of these cheap crystalline substances, made from common ingredients. Friend cautions, however, that the new perovskite displays aren’t yet commercially viable.
The materials in current semiconductor LEDs, including the organic versions, require processing at high temperatures in vacuum chambers to ensure the resulting semiconductors are pristine. By contrast, perovskites can be prepared simply by mixing their chemical components in solution at room temperature. Only a brief heat treatment is needed to crystallize them. And even though the perovskite crystals end up with imperfections, these defects typically don’t destroy the materials’ ability to emit light.
Read more