Israeli synthetic media startup D-ID wants to disrupt production of Hollywood movies with artificial intelligence.
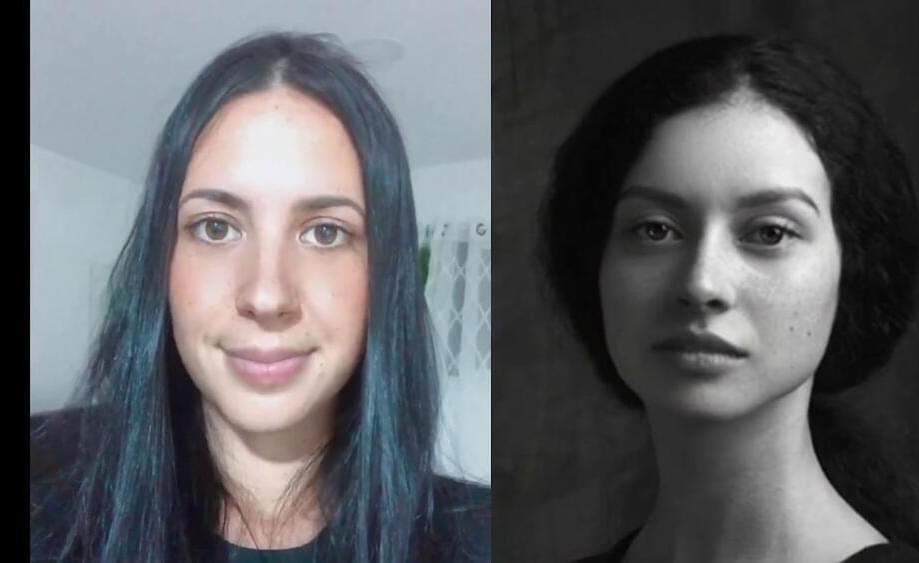
Israeli synthetic media startup D-ID wants to disrupt production of Hollywood movies with artificial intelligence.
IBM has announced its new chip, Telum – a new CPU chip that will allow IBM clients to leverage deep learning inference at scale. The new chip features a centralised design, which allows clients to leverage the full power of the AI processor for AI-specific workloads, making it ideal for financial services workloads like fraud detection, loan processing, clearing and settlement of trades, anti-money laundering, and risk analysis.
A Telum-based system is planned for the first half of 2022. “Our goal is to continue improving AI hardware compute efficiency by 2.5 times every year for a decade, achieving 1,000 times better performance by 2029,” said IBM in a press release.
The chip contains eight processor cores, running with more than 5GHz clock frequency, optimised for the demands of enterprise-class workloads. The completely redesigned cache and chip-interconnection infrastructure provide 32MB cache per core. The chip also contains 22 billion transistors and 19 miles of wire on 17 metal layers.
From voice-controlled personal assistants to smart robots on factory floors, Artificial Intelligence is having a profound effect on our lives. No surprise then that countries all over the world are trying to stay ahead of the curve. But when it comes to investment, who’s putting their money where their mouth is?
Looking at private funding, the United States leads the way — with well over 23 billion dollars going into the sector last year.
Coming in second is China, with almost 10 billion dollars. That said, Chinese state investment is particularly significant.
And the European Union falls far behind, with investment of just over 2 billion dollars.
So why is the EU lagging? And does Germany — its largest economy — have any plans to play catch-up? An example of AI in action can be found at a Rolls Royce control room just outside Berlin.
Robots destroy jobs and artificial intelligence will soon make us all superfluous. We’ve all seen headlines like that. But the reality of the situation looks a little different. Artificial intelligence is nothing more than a system that processes large amounts of data and makes predictions about the future based on that data. Engine manufacturer Rolls Royce has been a fan of AI for a long time.
Even in emergencies, it keeps its cool. In the control room at Rolls Royce just south of Berlin, safety engineers monitor more than 9,000 airplane engines worldwide. Long before the owners of the commercial jets would even notice a defect, the systems here sound the alarm. Artificial intelligence at work.
The systems are fed massive amounts of data. Then the owners of the aircraft are informed. The plane can then be taken in for maintenance long before the problem becomes expensive or life-threatening.
In the adjacent building, engines are assembled. Many parts are custom-made, previously developed by the design engineers, who also use artificial intelligence. For example, how would it affect the engine if certain components are changed? AI helps to find the best method.
The Center for Artificial Intelligence opened at the Dahlewitz site near Berlin in 2019. People here aren’t afraid that artificial intelligence will take their jobs.
In fact, the mechanics will probably have to install even more sensors and cables in the future. After all, in about five years’ time, the plan is for the aircraft to fly here with hybrid drive systems — based on sustainable fuel and electricity.
Subscribe: https://www.youtube.com/user/deutschewelleenglish?sub_confirmation=1
For more news go to: http://www.dw.com/en/
Follow DW on social media:
►Facebook: https://www.facebook.com/deutschewellenews/
►Twitter: https://twitter.com/dwnews.
►Instagram: https://www.instagram.com/dwnews.
Für Videos in deutscher Sprache besuchen Sie: https://www.youtube.com/dwdeutsch.
#ArtificialIntelligence #AI #RollsRoyce
AI has finally come full circle.
A new suite of algorithms by Google Brain can now design computer chips —those specifically tailored for running AI software —that vastly outperform those designed by human experts. And the system works in just a few hours, dramatically slashing the weeks-or months-long process that normally gums up digital innovation.
At the heart of these robotic chip designers is a type of machine learning called deep reinforcement learning. This family of algorithms, loosely based on the human brain’s workings, has triumphed over its biological neural inspirations in games such as Chess, Go, and nearly the entire Atari catalog.
Why do so many people get frustrated with their “high-tech” prostheses? Though sophisticated robotics allow for prosthetic joints that can do everything a human can and more, the way we control robotic machines right now doesn’t allow us to operate them as naturally as you would a biological hand. Most robotic prostheses are controlled via metal pads on the skin that indirectly measure muscle action and then make some assumptions to determine what the person wants to do. Whil… See More.
We plan to use MM to provide natural control over prosthetic limbs by leveraging the human body’s proprioception. When you wiggle one of your fingers, your brain senses muscle lengths, speeds, and forces, and it uses these to figure out the position of that finger. This is called body awareness, or proprioception. When someone receives an amputation, if their muscle connections are maintained with what is called the “AMI technique,” their brain still perceives muscle flexion as it relates to joint movement, as if their limb was still present. In other words, they are sensing movement of a phantom limb. To give an amputee intuitive control over a robotic prosthesis, we plan to directly measure the muscle lengths and speeds involved in this phantom limb experience and have the robot copy what the brain expects, so that the brain experiences awareness of the robot’s current state. We see this technique as an important next step in the embodiment of the prosthetic limb (the feeling that it is truly part of one’s body).
Notably, the tracking of magnetic beads is minimally invasive, not requiring wires to run through the skin boundary or electronics to be implanted inside the body, and these magnetic beads can be made safe to implant by coating them in a biocompatible material. In addition, for muscles that are close to the skin, MM can be performed with very high accuracy. We found that by increasing the number of compass sensors we used, we could track live muscle lengths close to the surface of the skin with better than millimeter accuracy, and we found that our measurements were consistent to within the width of a human hair (about 37 thousandths of a millimeter).
The concept of tracking magnets through human tissue is not a new concept. This is the first time, however, that magnets have been tracked at sufficiently high speed for intuitive, reflexive control of a prosthesis. To reach this sufficiently high tracking speed, we had to improve upon traditional magnet tracking algorithms; these improvements are outlined in our previous work on tracking multiple magnets with low time delay, which also describes how we can account for the earth’s magnetic field during portable muscle-length tracking. This is also the first time that a pair of magnets has been used as a distance sensor. MM extends the capabilities we currently have with wired-ultrasound-crystal distance sensing (sonomicrometry, SM) and tantalum-bead-based distance sensing via multiple-perspective X-ray video (fluoromicrometry, FM), enabling us to now wirelessly sense distances in the body while a person moves about in a natural environment.
It’s one of the most profound innovations of our time — and Manhattan-based Australian Kate Crawford wants us to wake up to AI’s inherent risks.