Nowadays almost everything is being 3D printed, so why should architecture be an exception? Many architectural firms are adopting 3D printing as their preferred technique to build structures. And 3D printed architecture is slowly but surely gaining a lot of popularity and momentum. This emerging trend is paving a path for itself in modern architecture. And I mean, no wonder, it has a ton of benefits! It’s a simple, efficient, and innovative technique that lowers the risks of errors, and also manages to save on time. 3D printing eradicates a lot of tedious steps during the construction process and simplifies it. It is being used to build homes, habitats on Mars, and even floating islands! The potential and possibilities of 3D printing in architecture are endless and mind-blowing. We’ve curated a collection of 3D-printed architectural structures that are our absolute favorites – from a 3D printed sustainable office pod to a 3D printed housing community for the homeless, every single one of these designs unleashes the magic and potential of 3D printing!
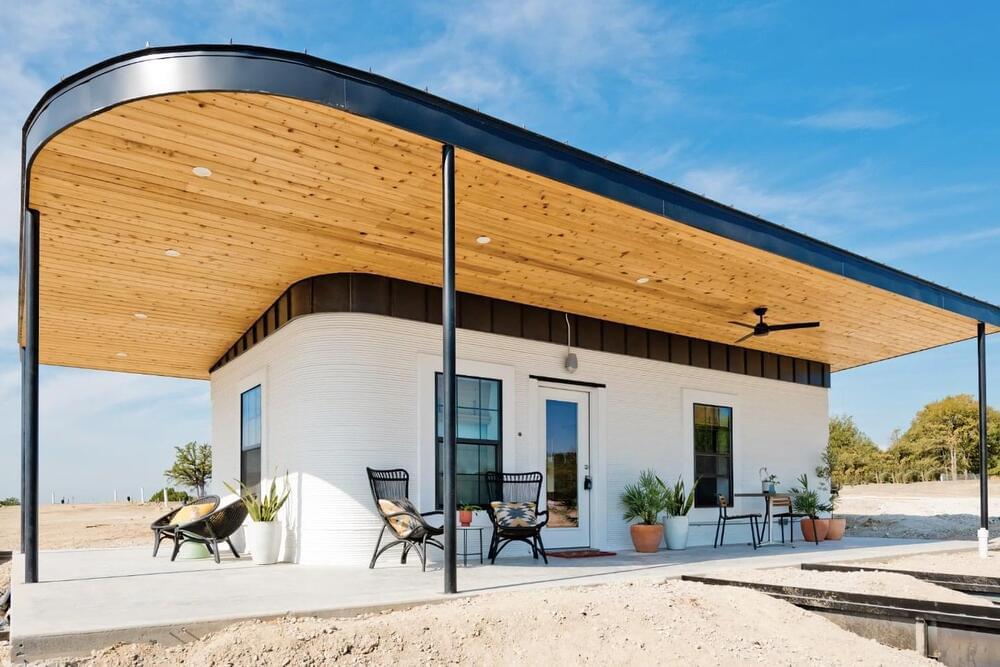