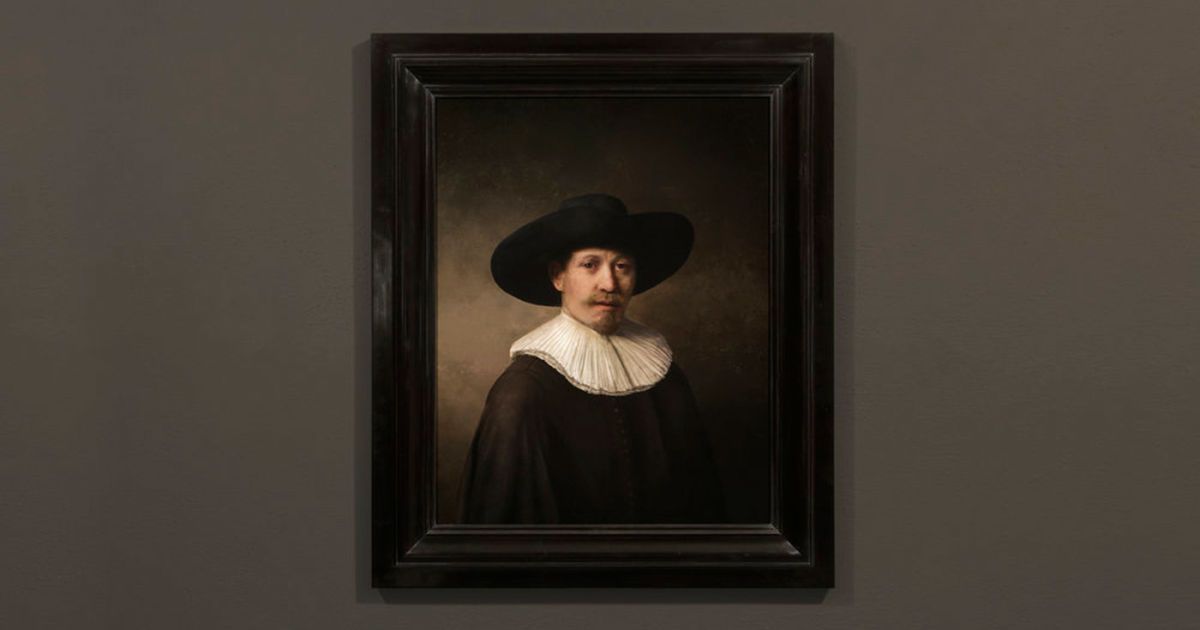
A new Rembrandt painting has been unveiled in Amsterdam on Tuesday, and we’re not talking about a newly discovered work. No, this one called The Next Rembrandt is truly brand new, created using data, algorithms and a 3D printer within the span of 18 months. A team of data scientists, engineers and scientists from various institutions, including Microsoft and the Rembrandt House Museum, joined forces to create this homage to the great painter. The team examined all the Dutch master’s known paintings to come up with the perfect project: a portrait of a 30 to 40-year-old Caucasian male with facial hair, wearing dark clothes with a collar and a hat on his head, facing to the right.
They then developed algorithms to extract what features make a painting a Rembrandt, such as the face’s shape and proportions. Ron Augustus, Microsoft’s SMB Markets Director, said: “You could say that we used technology and data like Rembrandt used his paints and his brushes to create something new.” To give their work a real painting’s texture, they used 3D printing techniques to print oil paint in layers. As a result, the portrait feels like it was actually painted by a human artist.
The project, which the Netherlands’ ING Bank commissioned ad agency J Walter Thompson to develop, most likely began as a promotional undertaking. As you can see, though, the final product turned out so good that the same technique could be used to make more affordable replicas (maybe even forgeries) of masterpieces.
Read more